Cement production is roughly 8% of global emissions, and the root causes are grounded in technical and economic complexities.
Cement is a fine powder which binds to rocks and hardens when water is added – this hardened product is concrete. It is the second-most consumed substance on earth, behind water, and will remain, for the foreseeable future, the key material enabling global infrastructure and housing.
The production of cement and concrete is a significant source of global greenhouse emissions however. Estimates suggest that production accounts for 8-10% of global emissions, or roughly 3x the emissions from global aviation hence the development of the cement and concrete innovation landscape map
Significant economic, regulatory, and technical concerns challenge the industry’s decarbonisation.
Figure 1: Global emissions from concrete productions versus all other sources1,2
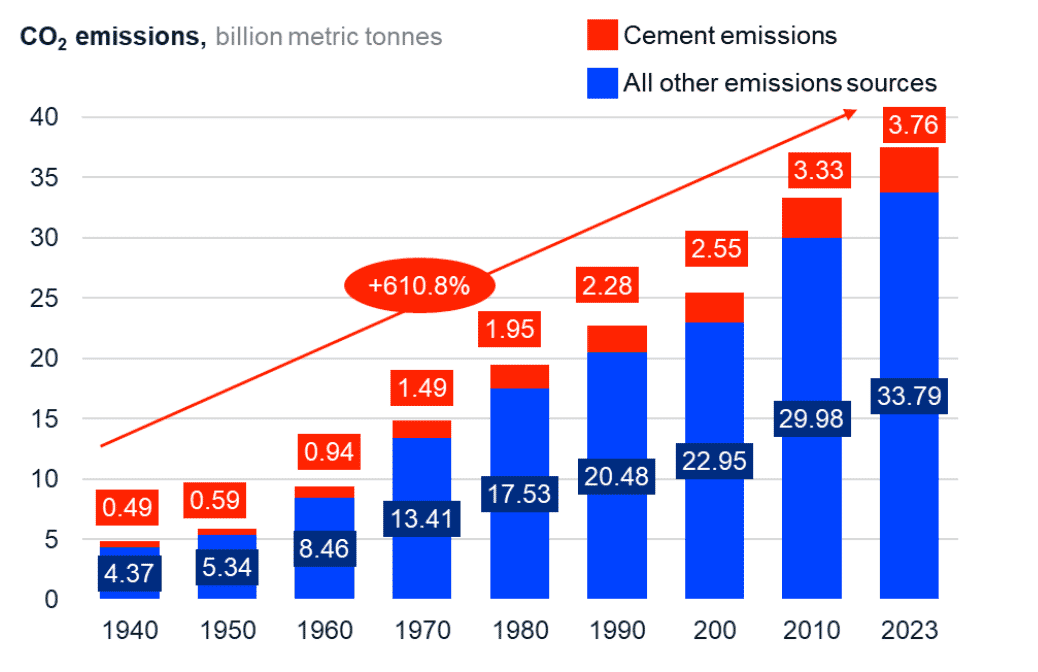
Technical: The production of the most common form of cement, Ordinary Portland Cement (OPC), causes significant emissions (the vast majority of the 8-10% listed above). This is in part because production requires burning fuel to heat kilns to significant temperatures (~1300C). Limestone, the basis of OPC, additionally emits CO2 as a chemical byproduct when in the kiln.
Economic: OPC-based concrete is ubiquitous, cheap, and highly commoditised. This is because its performance is exemplary, and its production is based on globally abundant materials (primarily limestone, water, and miscellaneous rocks) allowing for affordable localised production. As a result, suppliers differentiate on price, rather than on unique product offerings. Additionally, due to heat-up costs, it is most economic for cement kilns to remain on at all times.
Regulatory: OPC performs exceptionally well in structural and non-structural scenarios. As a result, key regulatory frameworks and standards require 70-100% of cement to be OPC, especially in structural use-cases, therefore severely limiting the market for non-OPC cements which may have lower-carbon production processes.
Figure 2: Emissions from cement production3
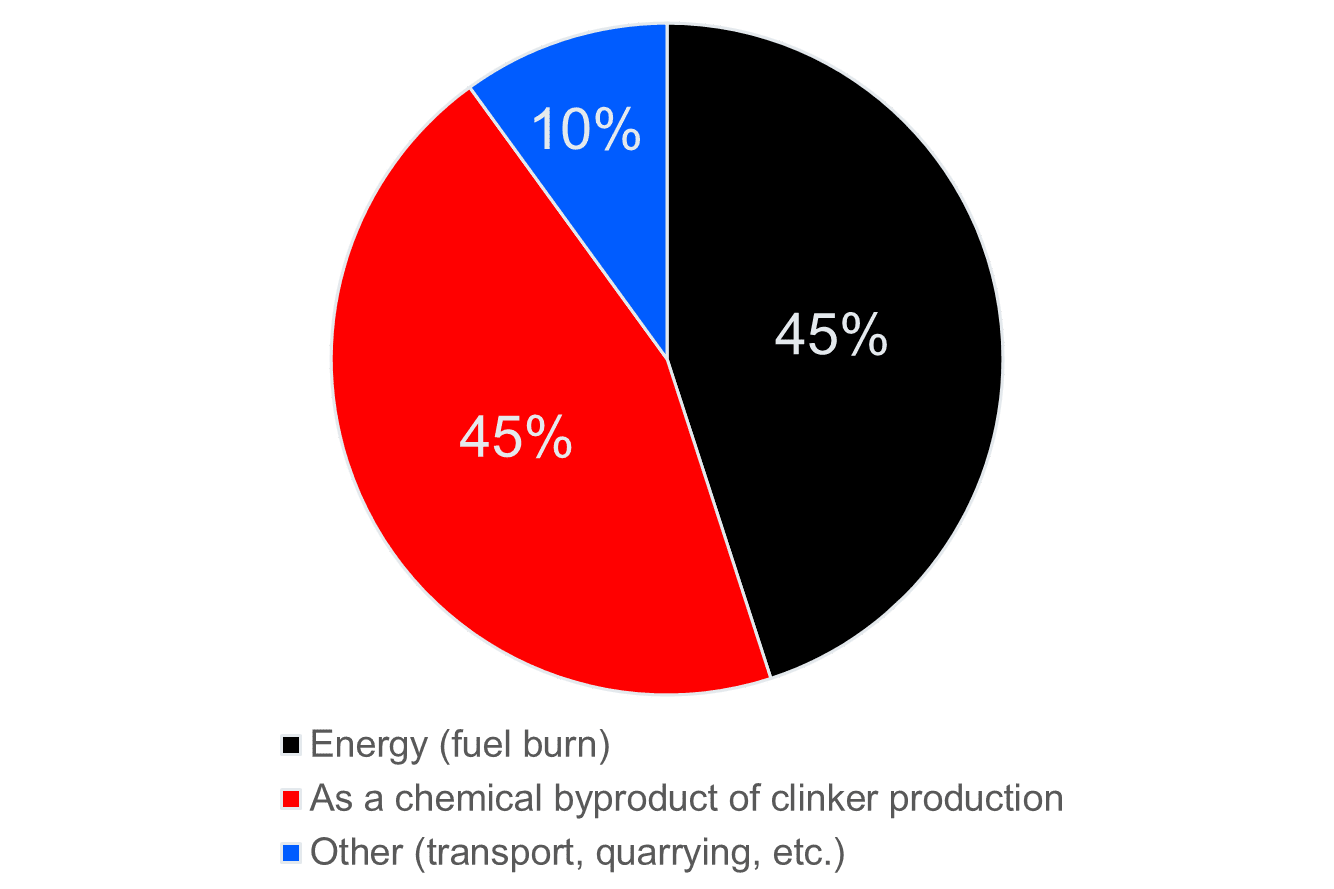
As a result of these challenges, in the UK’s construction industry, the “carbon gap” between current emissions trajectories and 2050 emissions targets is large and growing4. The growing demand for reliable building materials to accommodate a growing population threatens to widen this gap. As a result, manufacturers, suppliers and asset-owners need to implement, with haste, robust strategies to ensure technological relevance and regulatory compliance. The market for innovative next-generation products is already rising to meet this industry shift.
A landscape of global innovators have emerged who are revolutionising cement as a low-carbon technology frontier, challenging its status as a static commodity.
Concrete innovation tackling the cement carbon problem take three broad approaches.
- Produce cement with less energy
- Use cement and/or concrete more efficiently
- Use something else
- A different cement or;
- A different concrete altogether
This is roughly equivalent to Third Derivative’s taxonomy of “reduce”, “readjust”, and “reformulate.”
From a technical perspective, this results in seven key innovation categories:
- New clinkers: Alternative, low carbon ways of producing OPC, fully compliant with existing regulations.
- New Supplementary Cementitious Materials (SCMs; or clinker replacements): Cementitious materials that, under current regulations, can contribute a minority percentage (up to 30%) of cement mixes for structural, load-bearing components (such as buildings or bridges). The other 70% is OPC.
- Recycling technologies: New methods for recycling cement, concrete itself, or other waste materials for reuse as cement or concrete.
- CO2 sequestration: Innovations that enhance or utilise concrete’s intrinsic ability to lock away CO2 as it sets and hardens.
- Digital solutions: AI or advanced monitoring technologies that can make production or specification more efficient.
- Whole concrete replacements: Completely novel solid materials that can replace concrete outright.
- Performance enhancements: Chemical additives that improve the performance and longevity of concrete, thereby contributing to less production.
In the UK alone, 22 startups already raising private and public capital to accelerate commercialisation.
All categories of cement and concrete innovation are present in the UK alone.
Figure 3: UK cement and concrete startups by technology category
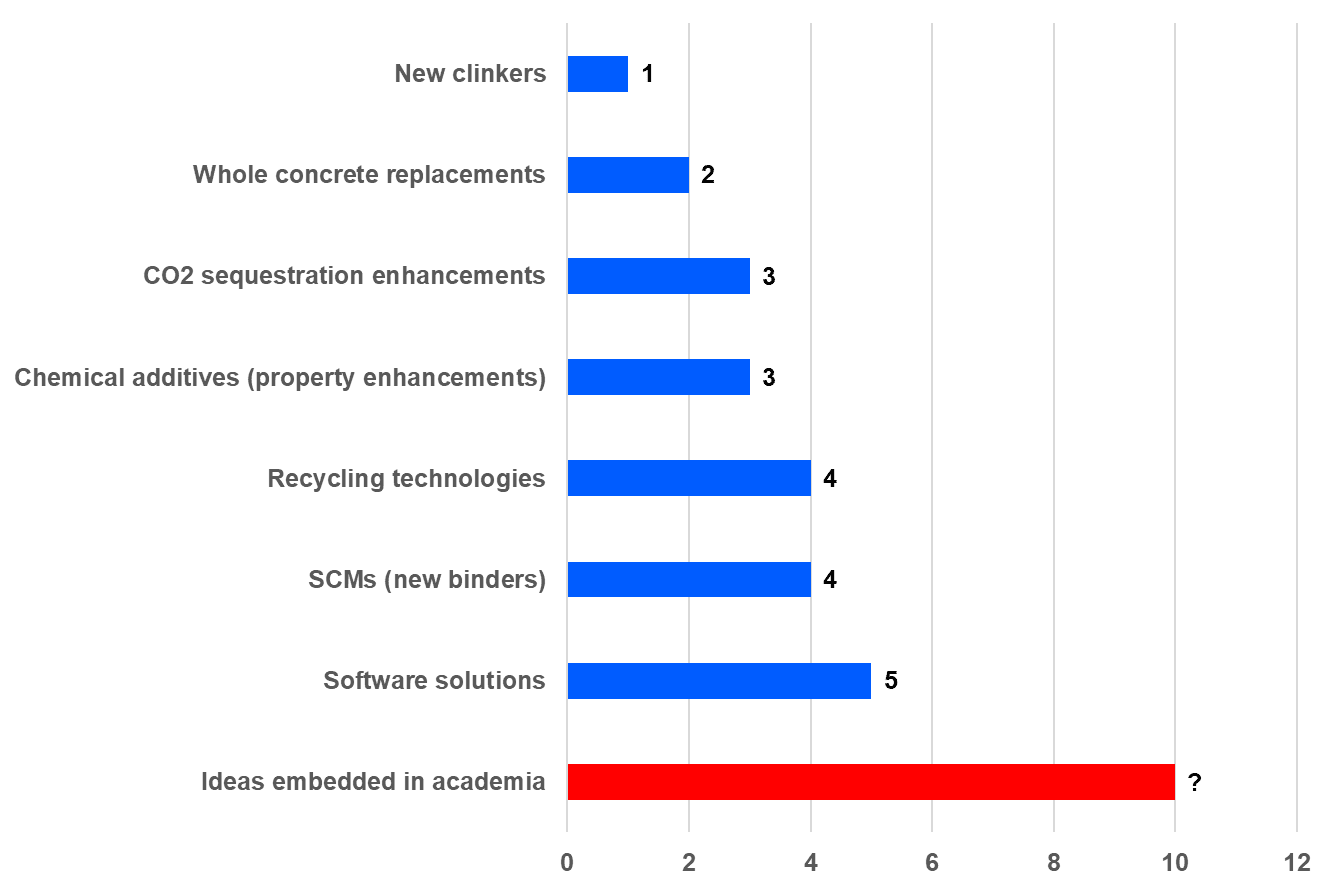
The resulting landscape of UK cement and concrete innovation emerges.
Existing innovation in cement and concrete has significant potential to disrupt existing supply chains
Of the different innovation segments present in the UK, new cementitious materials have the most decarbonisation potential and are a threat to industry status quos. New clinkers face few regulatory hurdles.
Figure 4: UK cement and concrete innovation landscape5
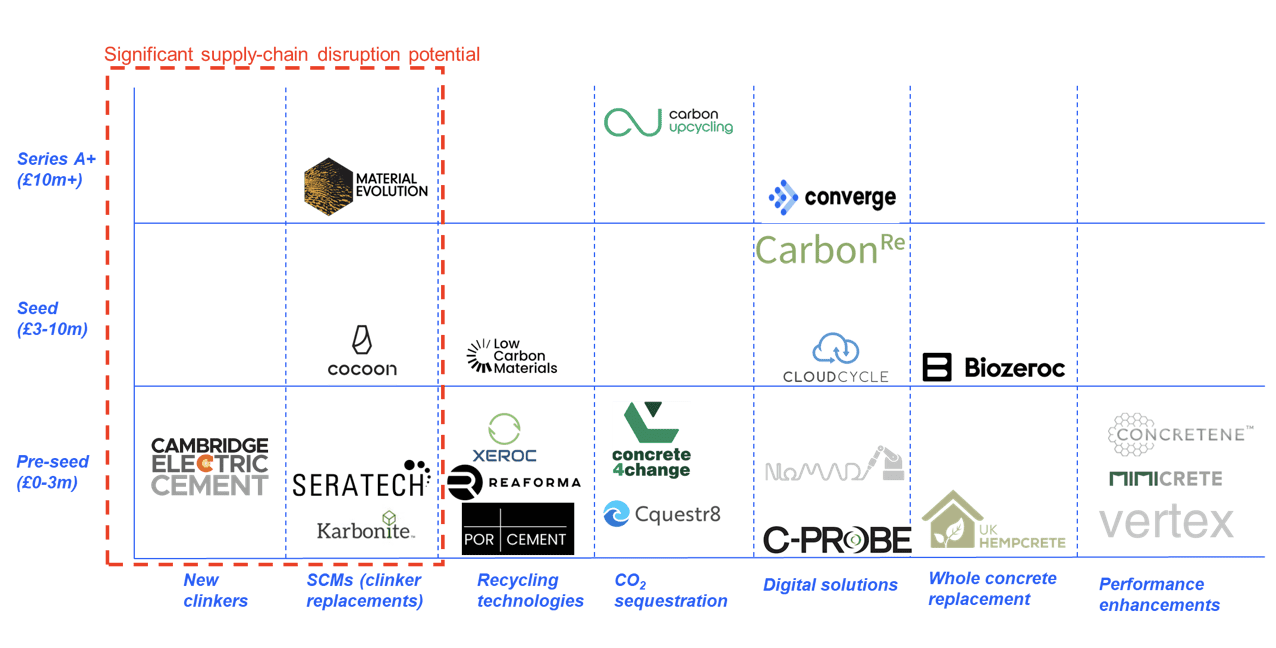
And if cement is decarbonising, every industry is.
It doesn’t get more difficult than cement. From materials to chemicals, manufacturing to logistics, every sector must rethink how it operates to remain competitive in a carbon-constrained future. The cement industry exemplifies this challenge, balancing the demand for essential goods and services with the need to cut emissions. Similar pressures are reshaping markets across the board, with new technologies, regulations, and shifting customer expectations driving the next wave of industrial transformation.
The cement industry is at a pivotal moment. As regulatory pressures tighten and innovation accelerates, corporates must act swiftly to integrate next-generation solutions into their supply chains. Whether through lower-carbon materials, digital efficiency tools, or breakthrough recycling technologies, businesses that adapt now will not only mitigate risk but gain a competitive edge in a rapidly evolving market.Our expertise lies in helping corporates navigate this transformation. By identifying the right technologies, optimizing implementation strategies, and ensuring seamless integration, we enable businesses to future-proof their operations. Get in touch today to explore how your company can lead in the low-carbon cement transition.
1Hannah Ritchie, Pablo Rosado, and Max Roser, “Breakdown of Carbon Dioxide, Methane and Nitrous Oxide Emissions by Sector,” Our World in Data, June 10, 2020, https://ourworldindata.org/emissions-by-sector.
2CLT analysis
3Johanna Lehne and Felix Preston, “Making Concrete Change: Innovation in Low-Carbon Cement and Concrete” (Chatham House, 2018), https://www.chathamhouse.org/2018/06/making-concrete-change-innovation-low-carbon-cement-and-concrete.
4Climate Group, UK LCCG, and Green Construction Board, “Decarbonising the UK Concrete Industry: Closing the Emissions Gap (Phase 1 Scoping Study),” October 2024, https://www.theclimategroup.org/sites/default/files/2024-10/Climate%20Group%20-%20ConcreteZero%20and%20LCCG%20-%20Closing%20the%20UK%20Concrete%20Emissions%20Gap%20Report.pdf.
5CLT analysis
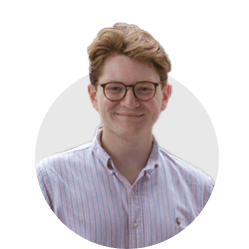
Written by